Why Prescriptive Actions Are Required to Realize the Expected Value of Predictive Alerts
With the automation of industry, sensors in equipment have become ubiquitous to control the production process. These sensors create enormous amounts of data, and in this Industry 4.0 era, we put this data to good use by merging and storing it in Historians and Data Lakes, and by combining the data with Artificial Intelligence tools to predict a machine’s behavior.
Current expectations are to be able to replace classic fixed time interval asset strategies, like a calendar-based equipment overhaul, with predictive strategies, where we only do maintenance activities when the predicted condition of the equipment requires maintenance or repair.
The goal of Asset Performance Management (APM) is to ensure asset compliance, performance and sustainability across the asset life cycle. We are moving from a “push” asset strategy, where we plan preventive interventions regardless of the immediate asset condition, to a “pull” asset strategy, where we trigger preventive interventions “Just-in-Time” (JIT) to avoid failure and unplanned downtime of critical equipment. The big advantage to this strategy is that we will avoid failures and unplanned downtime and save preventive maintenance costs and planned downtime, because we will be more effective by focusing on those assets that need intervention most.
Prediction with Data Analytics in Asset Performance Management (APM), promises a lot – but on its own, it is not enough to reach its full potential. Predictive alerts require specific prescriptive follow-up actions to realize the expected value.
I have witnessed several Owner Operators (OO) who are leaders in their industry, and most of them are at an advanced APM maturity level, where this phenomenon has become evident: They implement predictive alerts but are not realizing the value that they expected.
Operators or technicians are overwhelmed by the sheer number of alerts and they do not have the tools to prioritize concurrent alerts. They also do not understand how urgent each alert is and if they need to take extraordinary measures to avoid the predicted failure. All this makes creating a feasible and risk-based maintenance schedule a daunting task.
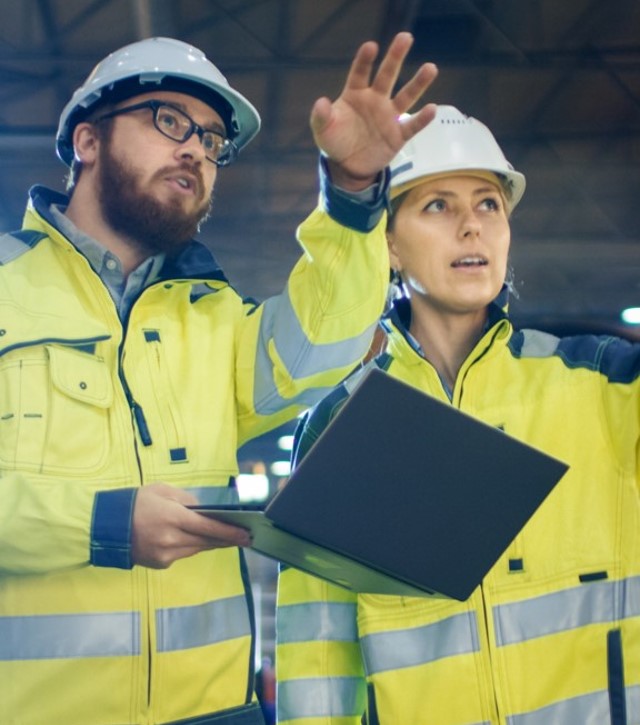
In some cases, required spare parts to solve the alerted problem are not available and even expediting them would not avoid expensive unplanned downtime. In other cases, precious time was spent to interpret and diagnose the alerts and to reach consensus on what action to take. Time that should have been spent on solving the problem.
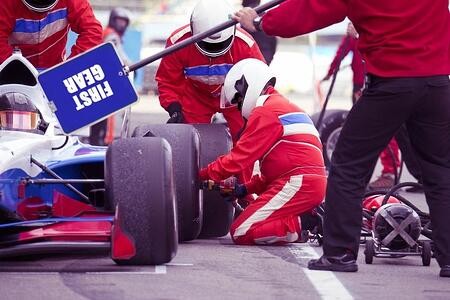
Prescriptive Actions are about implementing a “pit-stop” mentality to effectively solve alerted problems before they cause equipment failure. If you want to successfully transform your APM methodology from “push” to “pull” asset strategies, where we trigger events with alerts rather than plan them in advance, this requires careful follow-up action preparation and an agile organization to execute these actions.
We need to prescribe the following four elements for each alert that we predict:
- Criticality: What is the financial impact of this predicted failure? Impact is the total effect of the event if the predicted failure mode occurs.
- Urgency: How much time do you have? Urgency is a reliable prediction of when the failure mode will occur once the indicator alarm is triggered.
- Action: What action will you take? It defines the tasks you need to execute and includes the required skills, tools, permits, work instructions, and required asset safety isolation (i.e., lock out/tag out, or LOTO).
- Spare Part Management: Having the right spare part on hand determines whether a predicated failure can be avoided before it occurs.
Predictive Analytics enables us to define meaningful indicators that are based on sensor and other operations data. These indicators are true “lead indicators” in that they allow us to make decisions in real-time that will influence the performance of our Asset before it happens. This is quite revolutionary in the history of management systems. But unless we add prescriptive actions to these alerted indicators, we will not achieve the value that we expect. In the worst case, all the alerts could create nervousness and inefficiencies in the organization with detrimental consequences.