The connected factory network is the future of manufacturing operations
Adopting digital and data technology across distributed manufacturing networks supports efficiency and flexibility gains. Connecting these factories in the cloud creates a powerful network effect that further maximizes those benefits, says Rob McGreevy, Chief Product Officer, AVEVA
Manufacturers increasingly need to contend with increasing competition and continuing supply chain delays while facing pressure to reduce costs and operate more sustainably.
Running multiple production facilities in different locations brings several advantages in current operating conditions. Besides increased agility to adjust production based on local demand or supply chain fluctuations, distributed – or multisite – manufacturing also supports economies of scale and can facilitate access to new markets.
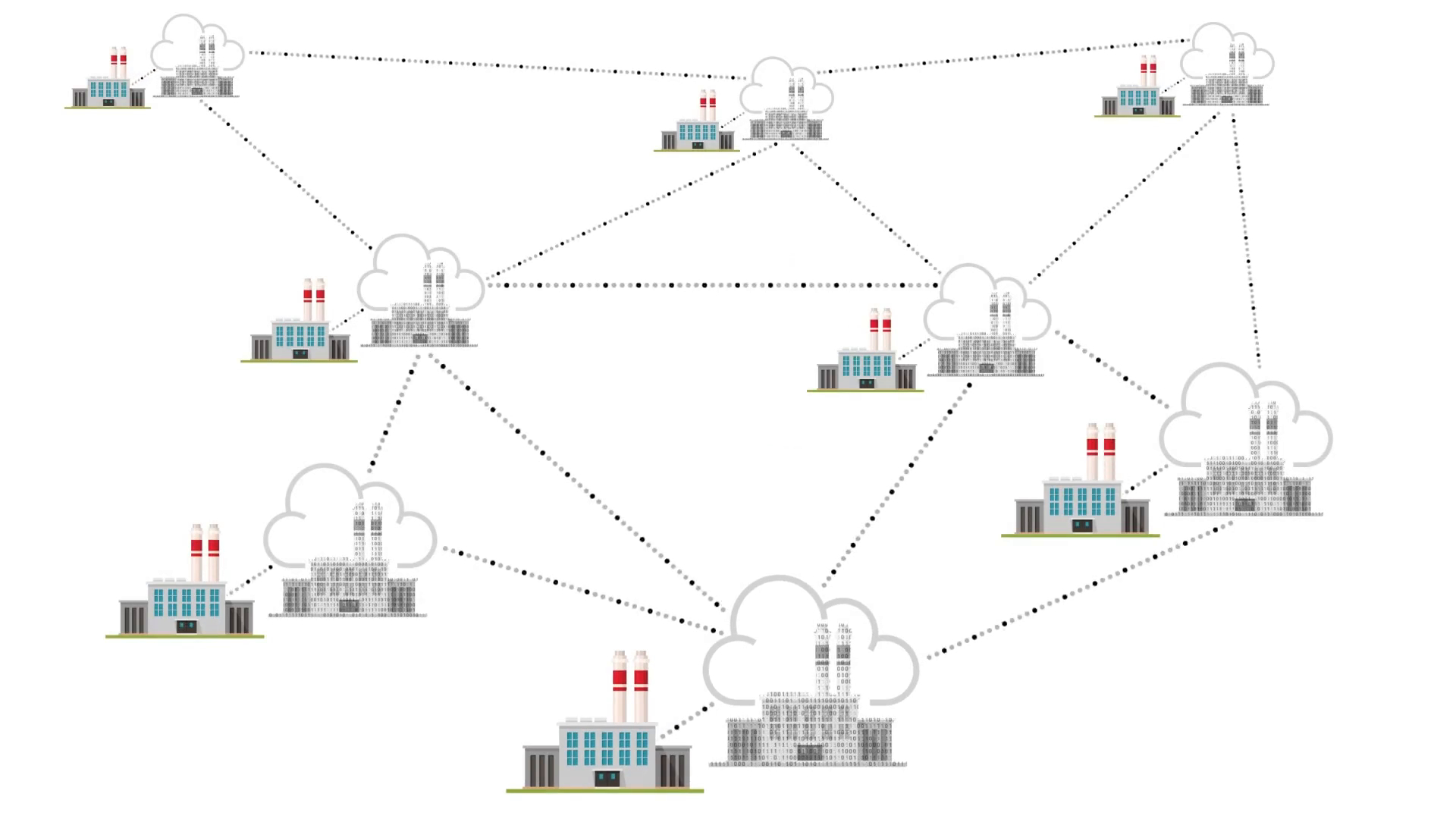
Running multiple production facilities in different locations brings several advantages in current operating conditions. Besides increased agility to adjust production based on local demand or supply chain fluctuations, distributed – or multisite – manufacturing also supports economies of scale and can facilitate access to new markets.
Digital solutions such as Manufacturing Execution Systems (MES) have proved their value for producers of all kinds of goods, both before and during the pandemic. A MES is a software application that manages all manual and automated workflows, and tracks the entire manufacturing process in real-time, from raw materials to finished products. This end-to-end visibility of the value chain in turn improves plant efficiency, quality control, waste reduction, cost savings, and sustainability.
Factories have noted gains from automated production processes, Industrial Internet of Things (IIoT) devices, paperless manufacturing, and data-driven continuous improvement for several years now. These have been the mainstay of MES systems.
The multi-plant networks most companies operate have largely been created by mergers and acquisitions. These facilities consequently often use a wide variety of operational technologies and practices top produce similar products.
Since a MES is critical for plant operations, businesses have traditionally deployed a separate MES at each individual plant. But such local deployments risk creating another information silo when customized to local plant needs, rather than following a standardized approach to how the plant is represented towards the business and supply chain functions.
Now, new technologies such as cloud and edge computing paired with global network reach and performance make it possible to centrally host a single MES for multiple plants. Such an ‘enterprise MES’ drives consistent manufacturing practices across geographies by standardizing technologies and processes in areas such as production reporting, continuous improvement, measuring plant efficiency and enforcing regulatory compliance.
The latest MES systems support running application services and data stores in the cloud, as well as connecting plant workers and automation systems remotely. This drives value, efficiency and sustainability gains across the entire plant network, unlocking higher level benefits at the business level.
The rise of industrial intelligence as a service
By leveraging the cloud to eliminate data silos between information technology, operational technology and engineering technology, industrial enterprises can create a powerful network effect.
At AVEVA, we refer to this technology as industrial Intelligence as a Service (IIaaS).
IIaaS forms the core of a new kind of connected industrial economy. With a single version of the truth available to all authorized stakeholders, enterprises can share data and insights from analytics both internally and externally, collaborate to create new opportunities, and solve the most critical challenges for industry and our planet.
In support of IIaaS as the backbone of the connected industrial economy, AVEVA enables businesses to drive multisite MES solutions simultaneously and consistently across connected plants. With the new AVEVA Manufacturing Execution System 2023, manufacturers can accelerate their digital transformation and closing the business-to-plant collaboration gap.
The competitive advantage in the post-pandemic era
In the post-pandemic era, manufacturers’ success will be defined by their ability to be agile and resilient in the face of change.
A global overview of manufacturing operations brings competitive advantages, leading to improved profit and sustainability outcomes. Multisite MES systems provide the necessary standardization for consistent visibility and reliable data-driven decision-making for distributed manufacturing operations.
By making this rich and contextualized operational data available from edge to enterprise, manufacturers can improve their business agility and supply chain resilience with consistent visibility into plant operations in real time. Operational best practices can be captured and scaled across all plants in order to optimize operational efficiency, reduce waste and energy consumption, and identify carbon emissions. The cost of quality and consumer safety compliance risks can be reduced thanks to consistency in product genealogy record keeping and end-to-end material traceability across the plant network.
Consumer goods company Henkel realised just this sort of gain when it built a digital backbone for its laundry and home care production business. The company deployed AVEVA MES and AVEVA System Platform towards meeting its sustainability and efficiency goals. As a result, it was able to improve supply-chain resource efficiency on the production side by 5-6% annually.
With such a critical impact on multiple levels of the manufacturing value chain, harmonizing operational technology, applications, and data across a multi-site manufacturing business is essential to building out competitive advantages while delivering on sustainability goals.