How can digital engineering drive the chemical industry’s green credentials?
Written by Fernanda Martins, Global Marketing Manager, AVEVA
The chemicals industry is under ever-increasing pressure to drive circularity and deliver on tough environmental targets. New sustainable products have moved beyond being desirable to being critical if the industry is to reach sustainability targets while remaining profitable. Many chemical companies have processes that are over 70 years old and have been optimized across decades. Their challenge now is to develop new processes that are even more efficient than the previous ones while addressing the sustainability issues: increase recyclable content and reduce emissions and waste.
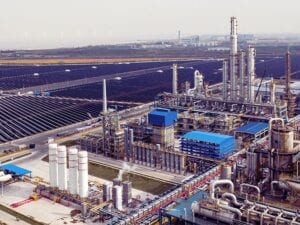
The connected plant of the future is nearly here. Are you ready?
Visit our Engineering the Plant of the Future page to learn more how your plants can meet the future with innovation, flexibility and resilience.
The forward-thinking Eastman Chemicals is over 100 years old and has developed the digital factory of the future long before the pandemic. Eastman invested in a platform called SEIGA (Seamless EPCom Integrated Global Access) to replace legacy engineering documents with a data-centric system to provide teams with instant access to accurate, reliable, and secure data which increased collaboration, agility, and efficiency. The move, which is now being rolled out around the globe, guides decisions throughout the value chain. With the higher efficiency levels achieved, Eastman engineering team uses SEIGA to:
- Continuously increase the recyclable content in their products
- Fast react to new market demands producing new processes and products within the sustainability targets
- Handover a reliable digital plant to operations
Learn more about the Eastman story.
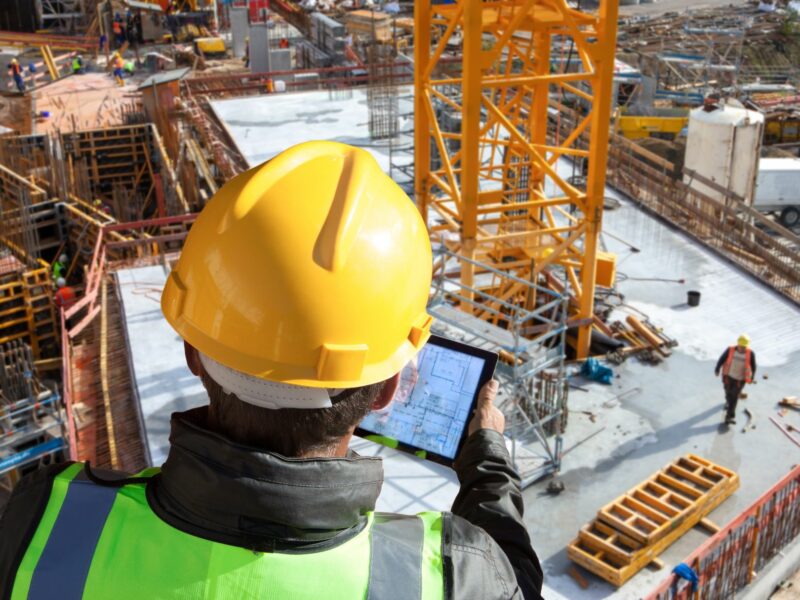
Digital transformation holds the key to engineering the chemical plant of the future
In the drive to be more efficient and sustainable, chemical companies and their EPC (Engineering, Procurement, Construction) partners can deliver capital projects more quickly and cost-effectively by digitalizing both greenfield and brownfield projects, and operations to drive optimal performance. Using a reliable digital twin strategy from the earliest phases of projects has been shown to halve the time in front-end engineering design (FEED) stage and reduce simulation efforts by 50%. In operations, the digital thread weaves back to engineering to inform potential process improvements and optimize maintenance and brownfield projects.
Start to build the chemical plant of the future now
At the heart of creating a reliable digital twin is a data-centric approach based on trusted engineering information management. It collates and verifies all project data from the outset and connects 1D, 2D, and 3D engineering data tagging them to the relevant plant assets. For brownfield projects, existing information can be digitized and supplemented with a laser scan of the plant to rapidly provide an accurate ‘as-is’ 3D model. With trusted data at their fingertips, engineers can test, repeat, and improve multiple times over – enabling faster product development cycles and optimizing processes.
The cloud-enabled digital twin aligns all teams and disciplines around a single source of trusted data. It provides end-to-end visibility of the capital project, breaking down siloes and fostering a culture of trusted collaboration and innovation. In this way, risks, wasted resources, and unplanned downtime are reduced, decision making is improved, and a sustainable facility can emerge.
By connecting workers, decision making and improved workflows in the cloud, EPCs and Owner Operators can gain greater control over project execution. And by reducing the hours wasted by day-to-day firefighting and searching for and verifying data, engineers can shift their focus towards innovating and developing sustainable processes and products.
Another critical aspect towards achieving a sustainable chemical plant is having an accurate representation of the plant´s behaviour. A multi-purpose process simulation enables process engineers to easily analyze complex systems as well as introduce new processes. The new generation of process simulators allow much faster comparison of different scenarios based on the desired outcomes – from efficiency gains to safety improvements, to carbon impact, and finding the perfect balance between all three. These insights inform subsequent engineering phases to ensure the optimal plant is designed. Armed with trusted simulation insights that can be effectively updated across the lifecycle, process engineers can transform the way they solve problems and become more productive, collaborative, creative, and inspired.
Chemical industry players have a real opportunity to transform not only project delivery but the very plants themselves. The plant of the future will be sustainable, with every aspect optimized digitally to reduce environmental impact and enhance performance. Creating a reliable digital twin from the outset that uses the latest industrial software to integrate every project phase will be critical to achieving those aims.