Go Beyond Preparation for Better Automation Maturity
Assessing your organization’s automation maturity status is a critical early move in the digital transformation journey and doing so provides a helpful indication of the steps your company can make in realizing the benefits of a digital transformation. Too often, plant operations and manufacturers know they want to increase their efficiencies, but they fail to develop a workable plan, instead making uncoordinated efforts to improve their processes.
Just being Prepared is not Enough
Are well-informed operational decisions hindered by information silos, or some data is available but not shared effectively across functional teams? Is your company managing day-to-day processes, but struggling to standardize efforts and meet business or operational key performance metrics? If the answer to either of these questions is “yes”, your company is likely at the ‘prepared’ level.
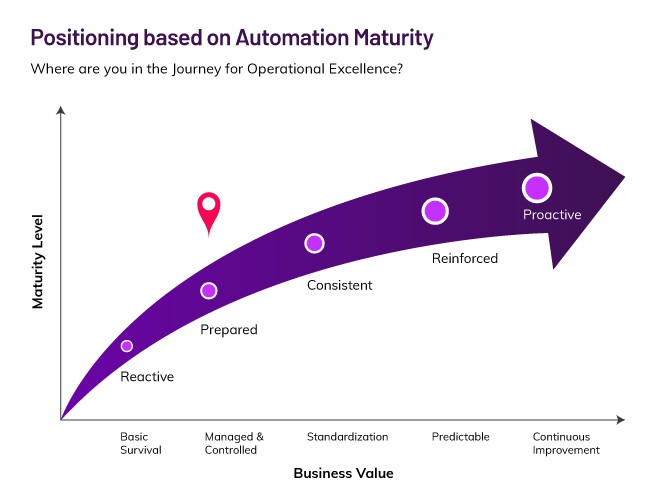
Your organization has consciously decided to invest in data-driven plant information systems to escape operations survival mode, and you may have already retired paper processes, reduced manual functions, and introduced automated data aggregation. However, comprehensive visibility remains somewhat limited across the organization. Process data, plant life management data, and enterprise scheduling and financial data are probably disconnected, making it difficult to see the whole picture of your facility’s health, and specific correlations between production and profit.
At this level, operations staff can intelligently respond to crises at the local machine level because data logging is in place. However, it is difficult to review the bigger picture to determine root causes because information is scattered across multiple repositories. Extracting insights requires a great deal of manual wrangling and analysis effort, and because it can be so tedious, production typically continues without adjustment until issues arise. Information silos make it nearly impossible to rely on proactive monitoring and optimization efforts for avoiding downtime.
These silos lead to localized decision-making, producing suboptimal results for the organization. The time and effort of manually accessing, cleaning, and correlating data from multiple systems ends up costing more than the value gained from the limited insights the disconnected data can yield.
Although reports are automatically generated in these prepared organizations, they may not contain full-picture information for making real-time business and operational decisions. For example, it may be impossible to draw connections between financial and operational procedures using data from a local machine process historian only, leaving staff to make their best guesses about the correlation based on gut instinct and experience.
Disconnected systems translate to complex operational training and IT management requirements because users must understand myriad types of automation systems present in a single plant. This can further exacerbate downtime due to delayed response and repair time, and it can present safety risks when less experienced personnel are required to address unfamiliar system issues.
Users may find themselves entering the same data in multiple systems—a frustrating experience that increases the likelihood of erroneous entries and makes it more difficult to keep track of where certain data is stored and used. These possibilities can also create operational inefficiencies if not managed prudently.
Moving Ahead
To advance beyond the prepared stage, companies must take steps to centralize and integrate data among their various systems in an organization-wide common repository. This eliminates data entry effort duplication, and it can drastically improve efficiency when analyzing data, viewing trends, and sharing insights. Interoperability between different systems, even those created by various manufacturers or established in different eras, reduces the training burden for staff.
AVEVA can help you centralize your data, improve situational awareness, implement standardization, and manage your varied systems through a common interface with modern industrial automation software solutions supporting many communication protocols.