Five ways the power industry can start engineering the plant of the future today
Written by Douglas Nunez, Sr. Infrastructure and Utilities Marketing Manager, AVEVA
The transformation of the power industry is as complex as it is rapid. Driven by a need to be more efficient, reliable, and sustainable, plants around the world are accelerating their digitalization.
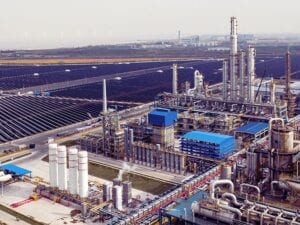
The connected plant of the future is nearly here. Are you ready?
Visit our Engineering the Plant of the Future page to discover how your plants can meet the future with innovation, flexibility and resilience.
With a clear government and public agenda for a move to renewable power sources, plant owners are under increasing pressure to demonstrate their green credentials. Last year 43% of the UK’s electricity needs came from renewable sources, with 17% of the United States’ electricity generation being from renewable sources in 2018**. While a full transition to renewable sources is at least two decades away, the decarbonization of the industry is a hot topic.
For the industry today that means treading a fine line between achieving operational excellence to optimize performance and profits while taking steps to reduce their environmental impact. Power Magazine’s senior associate editor, Sonal Patel, told a virtual conference recently that nearly 60 parent investor-owned utilities in the U.S. had emission reduction targets. More than 20 companies have said they will seek to achieve net-zero carbon emissions by 2050.
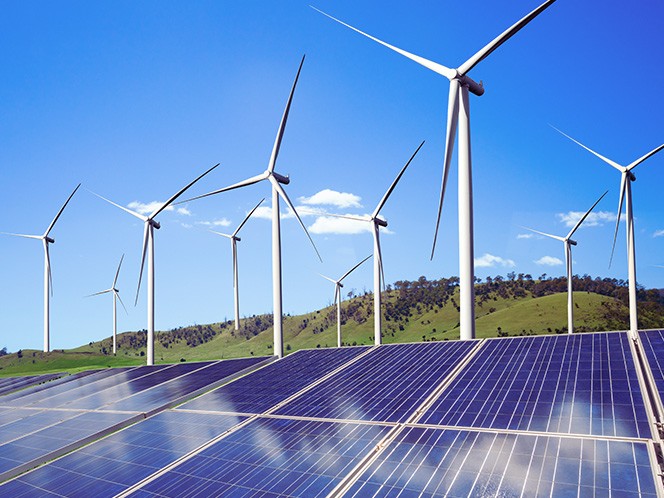
Digital twin solutions are empowering plant owners and their Engineering, Procurement, and Construction (EPC) partners to take steps today to engineer their power plants for a more performance-driven and sustainable approach for tomorrow – across existing operations, revamp projects, and new plants.
5 strategies for power companies to step confidently into the future:
1. Adopt a data-centric approach: Whether working on a greenfield or brownfield project, engineers who work in siloed or otherwise disconnected platforms and teams waste 50% of their time searching for and verifying information, and this doesn’t include the time spent reworking on errors made due to incorrect data. A system that harmonizes all design data including 1D, 2D, and 3D into a single trusted platform provides real-time actionable insights for complete end-to-end project and operational control, making it easier to spot project risks as well as opportunities to improve both project and operational outcomes.
2. Connect workers to enable connected decisions: Aligning all teams around a single source of trusted data builds better collaboration and improves performance. Decisions are made faster, risks are eliminated and wasted resources reduced. From initial design concept through to handover to operations, gathering and sharing quality data fast-tracks decision making – halving the FEED stage and reducing Total Installed Costs of the project by up to 4%.
3. Test, repeat, improve: Where EPCs and owner operators can reap rewards in the early stages of their future plant is through process simulation. Having a quality digital twin enables engineers to combine 2D and 3D modeling to test plant design and operations for optimal efficiency and sustainability. It can also help predict design or maintenance issues before they occur, improving safety and asset reliability. Once an operator has developed the culture, processes, and technology to optimize one plant it can be easily replicated across multiple assets.
4. Set sustainability as standard: Through cloud-enabled digital twin technology, owner operators and EPCs can leverage industrial artificial intelligence and machine learning to gain granular level insights across all phases of their plant from concept design through to operations. This allows capital projects to be streamlined and maximum value from the fleet to be extracted. By achieving operational excellence in this way, power plants of the future will achieve more with less, decreasing their carbon footprint through efficient resource consumption and less by-product waste.
5. Fail safely: A digital twin isn’t only for delivering effective capital projects and optimizing operations. 3D data in the digital twin can be leveraged to create an immersive virtual reality environment for field operator training where control room operators and field operators can practice together in a completely safe environment. A cloud-first operator training simulator is proven to be significantly more effective at supporting knowledge retention compared to traditional classroom-based learning, and it is faster and more cost-effective to roll out too. Operators can build muscle memory by practicing how to respond to emergencies in the safe environment of the digital twin, without risking plant assets.
As the power industry contends with challenges on multiple fronts, one thing is clear – optimizing performance by embracing digital twin solutions will be the cornerstone of achieving transformation.