Five ways AVEVA helps steel industry customers lower costs and increase returns on investment
AVEVA is having a moment, you might say, for its work in the steel industry. Fastmarkets, the cross-commodity price reporting agency, recently named AVEVA Technology/IT Provider of the Year for 2021. AVEVA acquired OSIsoft in 2021, bringing the industry-leading PI System into its portfolio.
Now, steel companies are using the industrial data management platform with AVEVA’s advanced applications like machine learning and artificial intelligence as part of one integrated portfolio to unlock new value.
9 out of Fortune’s Global 500 top 10 mining companies rely on AVEVA PI System to collect, contextualize, and analyze the data from complex assets.
Additionally, favorable steel prices in 2021 meant that many companies had more capital, and many chose to invest it in digital transformation. As a result, steel companies are achieving digital maturity at record speed and increasing their efficiency and profit.
Martin Provencher, AVEVA Global Industry Principal for Mining, Metals, and Materials, facilitated many of these digital transformations himself, and believes digitizing operations infrastructure is now more essential than ever for steel companies:
“In the last two years, I’ve seen the steel industry struggle most with asset reliability for critical assets, such as the furnaces, continuous casters, rolling mills, and even the transformers, which creates inefficiencies that increase costs and eat away at profits.”
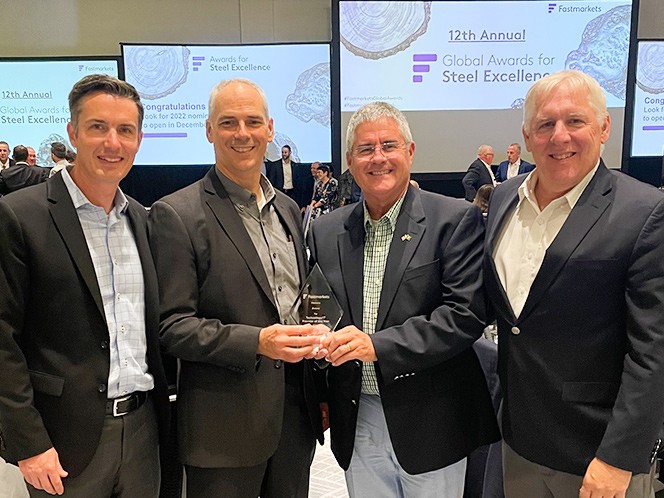
From left to right: AVEVA’s Jeffrey Murdock, Martin Provencher, Tom Richardson, and Tim Jeandron
accept the Technology/IT Provider of the Year Award at the Global Awards for Steel Excellence from Fastmarkets.
Reflecting on the digitizing frenzy of the last two years, and his decades of experience in the steel industry, Martin lays out the five critical ways steel companies lower costs and increase ROI using AVEVA products:
1. Energy management and efficiency
Because steel production is an energy-intensive process, energy use represents a significant portion of operating costs, especially in a market with unpredictable coal & gas prices. Maximizing energy use is top of mind for steel producers looking to reduce costs. The foundation for optimizing energy efficiency is access to real-time operational data to gain situational awareness of operations as a whole. This allows managers to make many small efficiency changes that add up when multiplied across the entire infrastructure and is a powerful tool for reducing unnecessary coal & gas costs. Documenting and maximizing energy usage offers another advantage. It can also help steel operations conform with forthcoming sustainability and environmental regulations.
2. Asset reliability
When steel companies rely solely on scheduled maintenance procedures, they can incur unnecessary additional costs—due to wasted personnel hours and unnecessary asset downtime—on maintenance that doesn’t yet need to be performed or can hurt production performance when assets go down unexpectedly. The need to know when to maintain and change bearings in their rolling mills, for example, becomes a significant cost in terms of time and money. By providing real-time information into asset health, an operational data management system can ensure that maintenance is only performed when needed.
Liberty Ostrava improved asset reliability in this way. By unifying its disparate systems on the PI System, the company automated its blast furnace tapping process and enabled predictive maintenance. Closely monitoring its blast furnace taps made it easier to calculate the burden being placed on them, and lowered temperature loss during run time. As a result, Liberty Ostrava used less fuel, improved quality by 15%, and cut production losses by 10%.
China Steel Group increased equipment efficiency by 50% by using condition-based maintenance techniques and improving asset reliability with AVEVA PI System. The company also saved more than 10% on maintenance costs and reduced accidents and losses by up to 20%.
3. Situational awareness with real-time operations data
A steel company that lacks a single source of truth for operations data can feel this keenly in costs associated with delays, bottlenecks, and operational inefficiency. Data locked away in silos presents a barrier to collaboration and problem-solving, which often worsens these inefficiencies.
When steel companies implement a data management platform like the PI System, the resulting insight gained can be leveraged to fine-tune the infrastructure, which can improve yield, cost cycle time, and protection of plant equipment. In this way, situational awareness across a company’s operations creates a foundation for continuous improvement.
When Essar Steel Algoma gained visibility into its operations and asset health with AVEVA PI System, it reduced unplanned delays in its Direct Strip Production Complex by up to 5%. This translated to a 140,000-ton production increase.
4. Cost savings and return on investment
Steel operators want to deliver the maximum amount of tonnage at the least possible cost. Monitoring the health of production assets in real time is the first, and crucial, step to keeping operating costs down on a digitalization journey. The savings many companies see when they invest in digital transformation often equates to a return on investment.
ArcelorMittal Dofasco saved millions after it integrated its condition monitoring software with the PI System. The company leveraged that data to get an accurate picture of equipment health to make more informed maintenance decisions. The company saved $1 million per year per furnace, projected a savings of $19 million in total, increased asset availability by 13%, and increased yield and quality by 15%.
5. The power of predictive analytics
A digital infrastructure that integrates advanced analytics, machine learning, and artificial intelligence for actionable insights can unlock even greater benefits. With advanced analytics for predictive maintenance, a company can know, for example, in advance when bearings in mill rollers will need to be replaced. Designed to reduce unscheduled downtime and maintenance costs, AVEVA™ Predictive Analytics provides early warning notifications and diagnosis of equipment issues before they impact operations. It combines data science with an in-depth understanding of physical assets, including a comprehensive prebuilt asset library.
“Having the ability to leverage machine learning and AI enables a steel mill not only to predict a potential failure, but really to know how much time an asset has left before it fails. AVEVA Predictive Analytics can even recommend proposed actions to optimize the life of the asset or improve its efficiency while it is still up and running. And these capabilities apply to more than individual assets. Steel mills can also apply predictive analytics for production optimization, energy efficiency, quality tracking, improvement, and much more.” – Martin Provencher
As Martin writes in Metal Market Magazine, predictive maintenance can reduce the time required to plan maintenance by 20-50%, increase equipment uptime by 10-20%, and reduce overall maintenance costs by 5-10%. Not only does predictive maintenance reduce costs, but it can also improve worker safety since asset maintenance isn’t conducted without good reason.