Connected Workers in the Power Industry
Written by Douglas Nunez, Sr. Infrastructure and Utilities Marketing Manager, AVEVA
The blog below gives an overview of Connected Workers in the power industry. For a more detailed report, read the LNS Research from 2020.
Just as the power industry was getting a handle on the different definitions for Digital Twin, here comes another buzzword: Connected Worker. The label by itself leads to confusion.
Are we not Connected Workers already?
Don’t most jobs require a level of connectivity?
It is helpful to come up with a broad definition of Connected Worker, but more importantly to define how it can help power utilities operate in a way that is sustainable, reliable, and profitable. In the broadest sense, Connected Workers refers to how we change the way we work. Connected refers to the technology enabler (Cloud, AI, ML, Mobility). Worker refers to anybody creating value for the business, not just the front-line worker. To further help us define Connected Worker, it is important to state what it is not: Connected Worker solutions are not about deploying more connected devices and cool technology.
The Connected Worker Value Curve
By presenting the Connected Worker Value Curve, LNS Research compares six sources of value by the degree of workforce connectivity and potential business value. The basic premise is that as the digital connectivity between people and their work environment increases, so too does the potential value to be gained. The curve is helpful because it allows us to think of Connected Worker as a spectrum rather than an abstract concept.
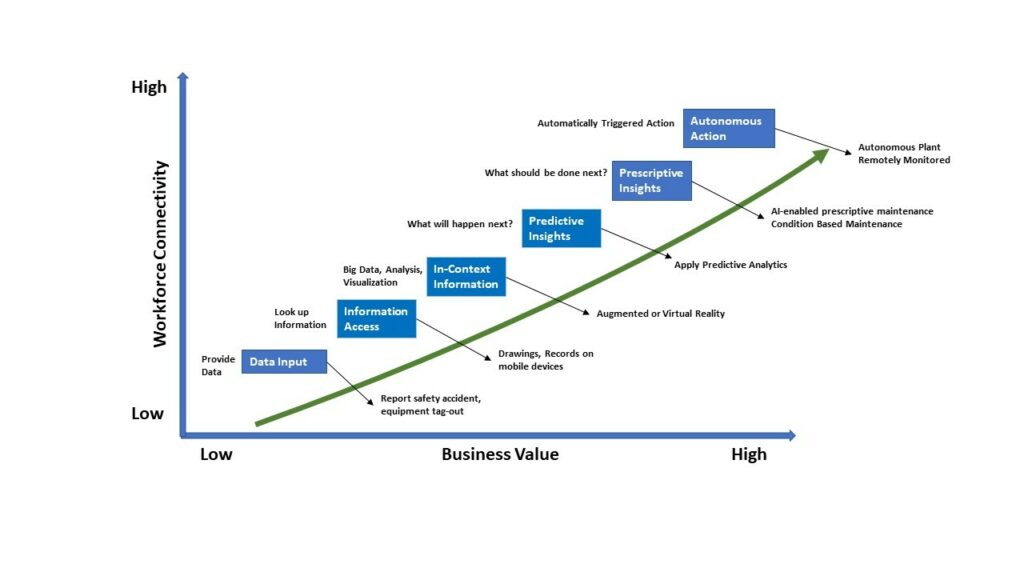
Some practical use cases for the power industry
1. Integrated engineering and asset information management relates to using an end-to-end integration of conceptual, planning, and detailed design into an environment that handles all process simulation and engineering from one single data hub. This can be used for either greenfield construction or modernizing projects.
2. Advanced process simulation uses first principle models to bring a superior level of robustness and accuracy to dynamic process simulation at your plant. The process models connect with other important plant applications, such as DCS and PLC control system emulators, to drive operator training systems. The addition of virtual/augmented reality leads to further gains in connectivity, and more importantly higher business value.
3. Asset performance management collects data about how equipment is performing and provides the tools and applications that enable the best use of assets. Performance monitoring along with predictive analytics enable condition-based maintenance insights into the cause-and-effect relationships between equipment conditions and failure modes. Predicting failures before they occur allows better outage planning, higher productivity, and reduction of Mean Time Before Failure (MTBF).
4. Smart field devices are equipped with extended operational and diagnostic capabilities. In most cases, these advanced capabilities are not utilized, because they are not made available to operators, or they require specialized software or personnel. Utilizing the full capabilities of smart field devices enables visibility into asset health, such as identifying a sticky valve before it becomes blocked or receiving an early warning that a motor’s power consumption is abnormally high.
5. Advanced Process Control (APC) uses artificial intelligence and neural networks to optimize fuel combustion, plant ramp rates, steam temperature control, and lower emissions among others use.
6. Mobile inspection rounds can be used for the execution of standard inspections with real-time analysis of operating variables to dynamically trigger proper actions. This ensures the operator performs the proper tasks, at the right time, correctly following the accepted procedure resulting in increased safety and reliability.
7. Contextualized actionable information facilitates the convergence between OT and IT systems, enabling a holistic view of plant operations that leads to faster and more informed decision-making.
In summary, we can see that Connected Worker is about problem solving and adding incremental value to how we work.